Wie gedruckt? In 3D mit Schilf!
Ersatz für erdölbasierte Kunststoffe braucht auch der 3-D-Druck. Wie Pflanzenfasern die Eigenschaften von neuen Werkstoffen dafür verbessern können, erforscht Wissenschaftler Jonas-Rumi Baumann an der Hochschule Bremen. Bei ihm kommen auch Paludikultur-Pflanzen wie Rohrkolben und Schilf in den 3-D-Drucker.
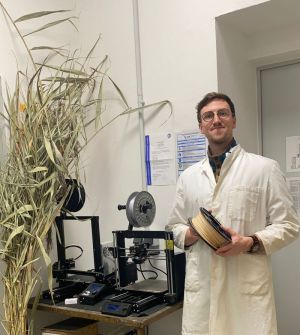
Herr Baumann, drucken Sie für Ihre Forschung ständig kleine Figürchen im 3-D-Drucker – wie muss man sich das vorstellen?
Das würde ich gerne, aber so weit sind wir noch nicht. Erstmal sind wir dabei, den Werkstoff für den Druck zu entwickeln. Mich persönlich fasziniert der 3-D-Druck. Wenn ein kleines Teil an meinem Kühlschrank kaputt gegangen ist, kann ich es einfach nachdrucken.
Was machen Sie dann genau?
Bei uns geht es um Compounds – um Verbindung von Kunststoff mit Biomasse, um so erdölbasierte Anteile in Produkten zu reduzieren. Pflanzenfasern können deren Eigenschaften verbessern. Solche Mischungen heißen „Naturfaserverbundwerkstoffe“. Ich untersuche diese neuen Werkstoffe an sogenannten Prüfkörpern - das sind Testteile - auf ihre mechanischen Eigenschaften. Wir haben schon mit Flachs, Hanf und Brennnesseln gearbeitet, sind aber immer auf der Suche nach neuen Fasern.
Und welche Paludikulturpflanzen eignen sich?
Breitblättriger Rohrkolben und Schilf eigenen sich bisher am besten. Sie haben die interessantesten mechanischen Eigenschaften. Dazu gehört die Steifigkeit, also wie stark sich etwas elastisch verformt und in die Ausgangslage unverändert zurückkehrt. Dann die Festigkeit: Was hält der Werkstoff aus, bis er bricht.
Papier und Kartonage - beispielsweise Formschalen aus Paludikultur-Biomasse - gibt es schon. Was ist für den 3-D-Druck anders?
Für Karton oder Einwegschalen muss die Biomasse ganz anders verarbeitet werden. Im Spritzgussverfahren, mit dem Kunststoffteile heute gängig produziert werden, kann der Rohstoff direkt in Granulat-Form verarbeitet werden. Für den 3-D-Druck müssen wir in einem zusätzlichen Schritt einen thermoplastischen Draht entwickeln und herstellen. Dieser ist einem langen Metalldraht ähnlich, der dann auf einer Rolle aufgewickelt ist. Beim Drucken wird er auf 200 °C erhitzt und durch eine Öffnung von 0,4 mm gepresst. Lage für Lage entsteht daraus das Werkstück. Dafür verwenden wir extrem fein gemahlene Biomasse, die in einem Compounder mit dem Kunststoff immer gleichmäßig vermischt werden muss. So sind konstant gleiche Eigenschaften des Produkts garantiert. Schon das ist schwierig. Hinzu kommt eine Veränderbarkeit durch Feuchtigkeit. 1-3% sind in Biomasse häufig auch nach dem Trocknen noch gegeben. Der Compounder ist eigentlich ein geschlossenes System, doch diese Feuchtigkeit muss unbedingt abgeführt werden. Sonst lassen sich die Bestandteile nicht richtig mischen. Dann kommt am Ende kein gutes Bauteil aus dem Drucker.
Wenn sich die Compounds verbinden – landen Ihre bisherigen Werkstoffe dann auf dem Komposthaufen oder in der Restmülltonne?
Das Ideal ist ein komplett kompostierbarer Verbundwerkstoff. Heute verwenden wir den Kunststoff Polyacetid (PLA), auch Polymilchsäure genannt. Unter Industriebedingungen etwa einer definierten Temperatur ist es kompostierbar, aber noch nicht zuhause im Garten. Ein anderer verwendeter Kunststoff ist das Polyhydroxybutyrat (PHB). Dieses baut sich zum Beispiel unter marinen Bedingungen ab. Das ist also gut gegen das Vermüllen der Meere durch Plastik.
3-D-Druck scheint noch eher eine Nische zu sein - wie sieht das wirtschaftlich aus? Gibt es einen Markt?
Die Masse Joghurtbecher wird man natürlich nicht im 3-D-Druck herstellen. Für große Mengen und eine schnelle Fertigung ist das Spritzgussverfahren geeignet. Auch dafür entwickeln wir einen Werkstoff mit Paludikulturbiomasse.
Beim 3-D-Druck geht es um geringe Stückzahlen, oft um das Herstellen von Prototypen im Heimbereich, in der Forschung und der Entwicklung. Es gibt immer mehr Drucker und deren Einsatz steigt. Damit wird es auch die Nachfrage nach biobasierten zukunftsfreundlichen Werkstoffen für den 3-D-Druck geben.
Kaufe ich mir irgendwann die Drucksubstanz aus Rohrkolben in der Kartusche?
Hoffentlich ja! Beim 3-D-Druck ist es dann eher eine Rolle. Es gibt bereits Compounds mit Naturfasern. Wir hoffen, dass ein Paludikultur-3-D-Druckdraht konkurrenzfähig sein wird, da er eine sehr gute Klimabilanz hat.
Jonas-Rumi Baumann arbeitet in der AG Biologische Werkstoffe von Prof. Jörg Müssig an der Hochschule Bremen. Die dortige Forschung zu Paludikultur-Biomasse für den 3-D-Druck ist Teil des Projektes NAPALU.
Das Interview führte Nina Körner.